Your Vision. Built to a Higher Standard.
Structural insulated panels (SIPs) deliver premium home performance that doesn't just meet your vision — but elevates it. Premier SIPS will partner with your architect and/or builder to bring your project to life.
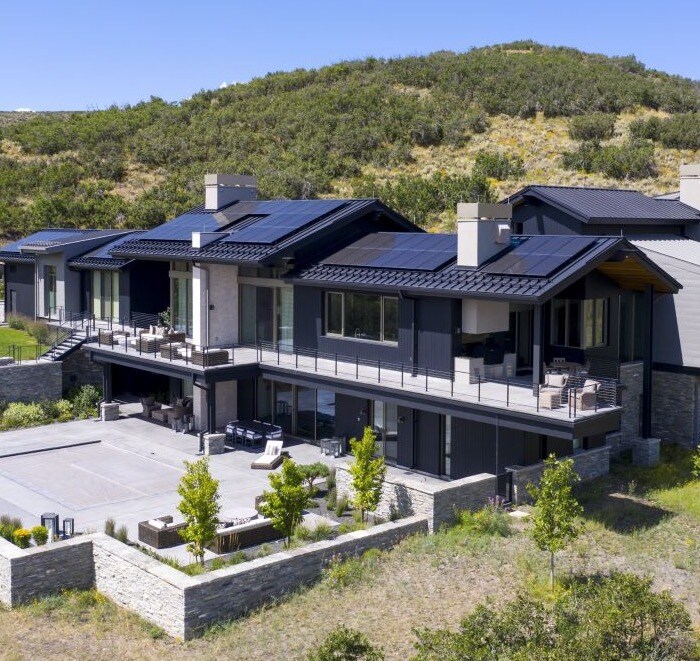
Your Healthier, Happier Home Awaits
Structural insulated panels aren’t just building materials. They’re the foundation of a home that protects, nurtures, and performs. SIPs create a strong, airtight envelope that keeps your family more comfortable, healthier, and safer year-round.
15 times more airtight than traditional stick framing, SIPs keep outdoor pollutants, allergens, and airborne irritants from entering your home, creating an incredibly healthy living environment.
Feel warmer in the winter, cooler in the summer, and cut energy bills by over 60%. Want Net-Zero, Passive House, or LEED? SIPs make it possible, and fast.
Cleaner air. Fewer allergens. No drafts. SIPs create a more comfortable space where you can breathe easier, sleep deeper, and live better every single day.
And beyond comfort, you’re building a legacy. SIPs use fewer resources and dramatically reduce energy use, giving back to the planet while giving more to your family.
Build a home that cares for you — and for the future.
Why Do Savvy Homeowners Choose SIPs Over Traditional Framing?
Choosing how you build your home is one of the most important decisions you'll make — and it pays to choose performance. Compared to outdated stick framing, SIPs deliver unmatched energy efficiency, strength, and durability. If you're aiming for a high-performance home that saves money, boosts comfort, and stands the test of time, the difference is clear.Energy Efficiency
SIPs are an exceptionally efficient system that save 60-100% on energy consumption. With a SIP home, you'll reduce your carbon footprint and make a lasting impact for the future.
Strength and Durability
Twice as strong as traditional site framed homes, SIPs homes are fire, earthquake, and hurricane ready, providing superior protection against natural disasters.
Long-Term Savings
More than a home, SIPs are a smart investment. With lower monthly energy bills, higher home values, and green home loan & insurance options, SIP homes pay you back, month after month.
Eco-Friendly
Eco-friendly by design, SIPs reduce construction waste, use sustainable, recyclable materials, and slash energy consumption. Build a greener tomorrow with a SIP home.
Speed of Construction
Factory-built panels install up to twice as fast as stick framing, so your contractor can build faster, cut labor needs, combat weather challenges, and keep your project on schedule.
Health & Comfort
SIPs improve indoor air quality by reducing drafts and limiting outdoor pollutants, while also providing quieter, more comfortable living spaces throughout every room.
Frequently Asked Questions
About SIP Houses
What is a SIP house?
A SIP home is a type of energy-efficient construction that uses panels made from a layer of rigid foam insulation sandwiched between two structural facings. They’re particularly popular in green building practices and among those looking to create sustainable, energy-efficient homes.
How long will a SIPs house last?
SIP homes typically have a lifespan of 50 years or more, depending on factors such as material quality, maintenance, and environmental conditions. Properly designed and constructed SIPs can provide long-lasting durability.
How much does it cost to build a SIPs house?
SIP home prices, just like stick-built homes, vary significantly based on location, material and labor costs, the size of the home, etc. Although the initial investment may be higher than traditional construction methods, many homeowners find that long-term savings in energy efficiency and lower utility bills can offset this cost over time.
Can SIPs be used in any climate?
Yes, their superior insulation properties make them suitable for both hot and cold environments. SIPs help regulate indoor temperatures, keeping homes comfortable year-round, regardless of external weather conditions.
How do SIPs affect heating and cooling systems?
SIPs enhance the energy efficiency of heating and cooling systems by providing superior insulation and minimizing air leakage. As a result, homes built with SIPs require less energy to maintain comfortable indoor temperatures, leading to lower utility bills and reduced strain on HVAC systems.
Take a SIP of Inspiration
Premier SIPS has been transforming homes since the 1980s, shaping thousands of dream homes across North America. With countless projects and videos to explore, you'll find endless inspiration for building a home that’s as unique and lasting as your vision.
What to Expect When Working With Premier SIPS
The timeline below serves as your guide to the house building process with Premier SIPS, outlining what you can expect throughout the lifecycle of your project.
Before our team can fully support you, you will need approved SIP house plans and a contractor for your project. If you do not yet have an Architect or Builder, we're happy to offer referrals from our extensive SIPs network.

Collaborate with your architect or designer to create your SIP house plans. You or your contractor can submit your approved home plans to your local Premier SIPS Representative, who will provide a Project Estimate within 5 to 10 business days.
If your Architect or Contractor has questions along the way, they should reach out to the local Premier SIPS expert in their area.

Sign and return your Project Estimate, which outlines the pricing information and terms and conditions for both parties. Please note that approval of the estimate requires a non-refundable deposit to begin the drafting and project management process.

You will be assigned a dedicated Premier SIPS Project Manager who will provide you with custom SIP Layout Drawings, typically within 10 business days of estimate approval.

Consult your Architect or Contractor to review the Layout Drawings for accuracy and approve them by signing each drawing in the set. This process includes two rounds of revisions, with any additional edits subject to extra fees. A "Layout Drawing Review Checklist" is available to assist in this process.

Your finalized and approved SIP house designs are converted into Production Details, which Premier SIPS uses to fabricate your panels. Additionally, your Project Manager will create a final Contract of Sale (COS). To initiate production, please sign and return the COS along with a 50% down payment.

Once the signed COS and down payment are received and cleared, your project will enter the production schedule. Because we do not sell uniform, pre-manufactured SIP home kits, any changes made after production begins may result in delayed shipment and additional charges.

Within 10 business days of your project entering production, the Premier Shipping Manager will reach out to confirm and schedule your delivery date. The final balance must be paid in full before shipment unless alternative arrangements have been made.

Review your COS for a detailed overview of your SIPs delivery. Unlike conventional framing, SIPs occupy a larger footprint, so planning for trucks to deliver pre-fabricated roof and wall panels during this stage will facilitate easier installation.

A representative must be on-site to receive the shipment and physically inventory the SIPs according to the provided packing list. If any items are missing or damaged, note these on the Packing Slip from the delivery driver and immediately inform your Project Manager for assistance.

Your custom-built SIPs are finally ready for installation! Be sure to keep your SIP home plans in a safe place on the jobsite, as contractors and installers will refer to these often.
Let's Connect
Already have SIP home designs and ready to move forward? Still have questions and want to learn more? Fill out this form and a member of our team will be in touch shortly.
Montana Manufacturing
15 Arden Drive
Belgrade, Montana 59714
Washington Manufacturing
18504 Canyon Road East
Puyallup, Washington 98375
Helpful Resources From Premier SIPS
The Latest From Premier SIPS
Accreditations & Affiliations
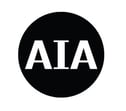
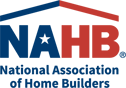


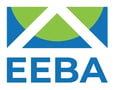
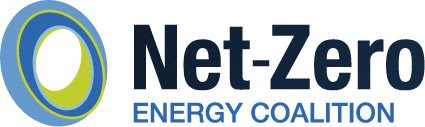
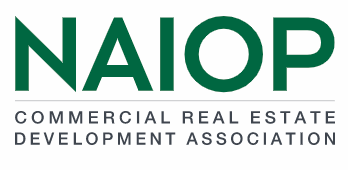
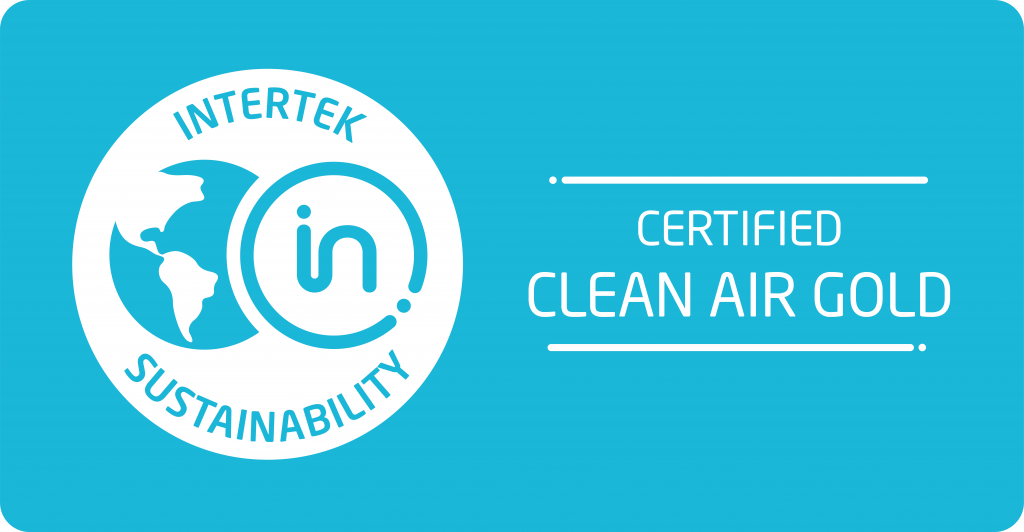
Find Your Local Rep
As the oldest SIP manufacturer, Premier SIPS offers a superior building envelope framing system for commercial and residential structures. Contact an expert in your region to discuss your next project or to explore the benefits and cost savings when designing and building with SIPs.