Apex Track Side Car Condo, AZ
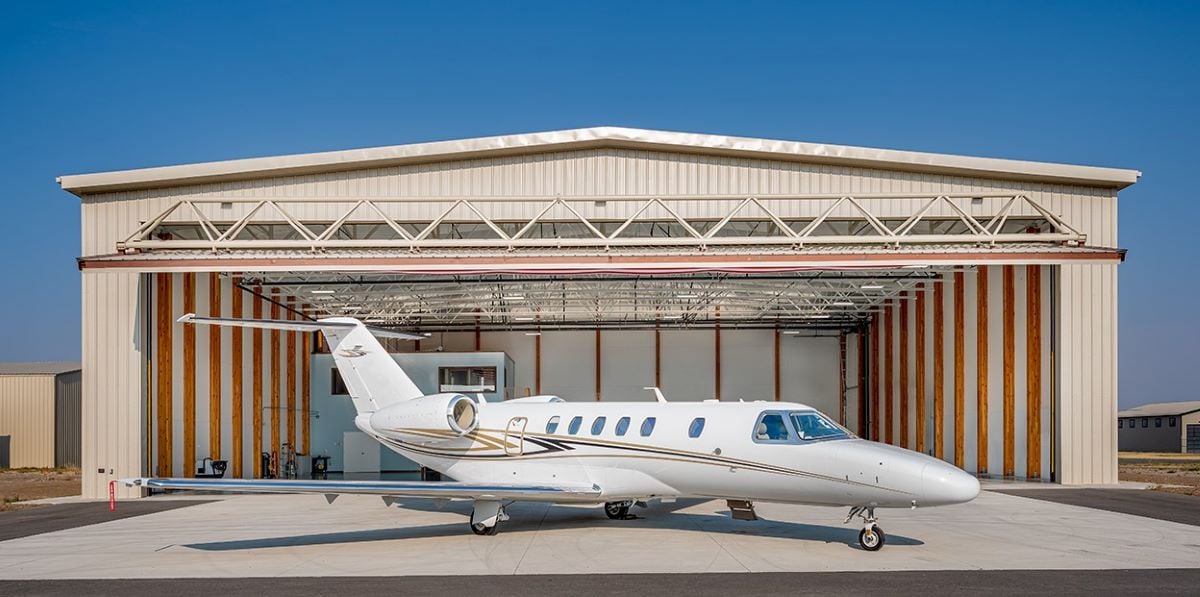
Commerical | Montana | SIPs Hangar
Montana
Project Type Commercial | Community Use
Year Completed 2020
Project Size 10200 sq ft
SIPS Used 8" Walls & 12" Roof
Sustainable Features Premier SIPS
Awards 2021 BEA Honorable Mention Classic Commercial Over 10K S/F
Architect RPA
Contractor
Project Overview
- Using SIPs allowed for expedited erection of the structure, resulting in lower labor costs.
- The resulting building is very energy efficient due to the high R-values and minimal thermal bridging of the SIP roof and walls, providing a better value compared to that of a manufactured steel building.
- Utilizing SIPs in combination with timber framing allowed us to maximize the embodied carbon in the structure, minimizing the use of steel, a high-carbon footprint material.
- Utilizing the interior SIP skin as a painted surface saved materials, adding to sustainability and rapid construction.
- Hangars are naturally devoid of a large number of windows and doors, so utilizing a product that serves more than one purpose (i.e. forms the shell and braces the building) provides greater efficiency of building materials compared to a manufactured steel building.
Innovative Elements:
- The higher-power hydraulic door system was a marvel in itself.
- The hangar door assembly is entirely self-supporting and does not rely on the structure of the building.
- The hangar door has a 3" SIP nail base plated to the inside of it.
- The Flying H hangar roof structure combines SIP roof panels with steel open-web joists to create a 100ft clear-span in two directions, designed to support a roof snow load of 30 lbs/sf.
- The 30' tall walls, with no intermediate floors to provide bracing, consist of SIP panels fastened to the outside face of 8-3/4" wide glued laminated timber columns ranging in depth from 9" to 16-1/2" (chosen due to the environmental benefits of using wood versus steel).
- Specially-designed joist seats were engineered to be compatible with the connection of the open-web joists to the ends of the timber columns.
- Special considerations were needed during erection; the tall timber columns were temporarily braced with masonry sway bracing and an 8ft tall “starter course” of SIPs around the base of the building.
- Carefully considering overhang dimensions and specifying typical column bay spacings of 8- and 12 feet allowed us to balance column sizes with allowing roof and wall SIPs to be unstiffened with internal lumber (even with high wind force demands on the panels), while virtually eliminating SIP panel waste, allowing the use of full-size 8ft x 24ft roof and wall panels throughout the majority of the structure.
- To increase the energy performance of the building, the owner chose to use thicker SIP panels than required structurally.
- Inside the building, a two-level enclosed structure measuring approximately 20ft x 20ft was built using conventional wood framing to house the mechanical equipment room, restrooms, offices, and a pre-flight plan room.
- A fire suppression system was provided.
- The hangar is located in a high-seismic region; moreover, with the very large door on one side, the structure was designed as a partially enclosed building. As a result, the design earthquake and wind forces on the structure are very high, requiring careful design and detailing to provide a load path for uplift and lateral forces.
- The lateral system is comprised of a SIP roof diaphragm, SIP shear walls (on three sides of the building), and a steel joist moment frame around the door.
- The unique moment frame is comprised of a specially-designed and detailed open-web joist with double-pitched top chords (limited in depth to provide maximum door opening height), supported by large wide-flange steel columns (size W24x103).
- Wood struts were engineered to brace the end walls and moment frame joist, and continuous wood members were provided around the perimeter of the building, at the roof level, to act as diaphragm tension and compression chords.
- The large hangar door is a center-pivoting vertical-lift hydraulic door measuring 90ft wide x 27ft tall, by Higher Power Hydraulic Doors. This unique door system reduces the forces imparted on the structure, versus the out-swinging hydraulic door systems typically used on hangars.
- The door was heavily insulated with EPS foam placed between the steel framing members for energy efficiency, and covered with a painted nail base (single-sided SIP panel) to eliminate thermal bridging and create the interior finish surface.
- The hangar slab was engineered to withstand stresses due to point loads imparted by large aircraft wheel loads.
- High-density EPS insulation was placed beneath the slab for energy efficiency; the EPS was modeled as a stiff subgrade supporting the slab, to correctly capture the behavior of the materials. The insulated slab is particularly important due to the use of radiant floor heating.
- Compared to a manufactured steel building, which is the conventional building system for this type of structure, this SIP building has a number of advantages (in addition to those described above).
- Special inspection costs were greatly reduced, due to far fewer field-erected steel connections.
- Additionally, cost savings were realized through significant reductions in foundation size, complexity, and a small crew of carpenters/laborers required to erect the columns and SIPs.
- From the user’s standpoint, this building is architecturally more attractive, and provides more usable space than a similar-sized manufactured steel building, due to the use of smaller column and joist members.
- Notably, this architecturally-appealing and energy-efficient hangar design could be easily repurposed for use as an events center, gymnasium, emergency shelter, or similar facility, in place of a more traditional manufactured steel or CMU building.
- The large door opening creates an opportunity to provide an interior space connected to the outside, with the ability to close the large hydraulic door to protect the users from inclement weather
HVAC: In-slab radiant heat is provided, utilizing a high-efficiency natural gas-powered boiler.
Related Portfolio
Find Your Local Rep
As the oldest SIP manufacturer, Premier SIPS offers a superior building envelope framing system for commercial and residential structures. Contact an expert in your region to discuss your next project or to explore the benefits and cost savings when designing and building with SIPs.