As wildfires continue to reshape communities and landscapes, the urgency to rebuild stronger and smarter has never been more apparent. Recovering from such devastation requires more than just replacing what was lost—it calls for innovative building strategies prioritizing resilience and safety.
Smart, science-driven fire-resistant construction can be the key to a home’s survival. By incorporating fire science into building practices, we can create structures designed to withstand the unique challenges of wildfire-prone areas. Structural Insulated Panels (SIPs) offer a forward-thinking solution, combining energy efficiency, durability, and proven fire-resistant features. They are specifically WUI (Wildland-Urban Interface) recognized for use in multiple fire-prone areas.
Keep reading for a comprehensive guide to the fire safety advantages of SIPs, offering architects, builders, and community leaders the insights and resources needed to construct safer, stronger structures. Together, we can focus on recovery by embracing solutions that protect lives, homes, and communities for the future.
⇒ SIP Project Highlight - California Residential Fire: This project was in the middle of a major wildfire and the original house was destroyed. By working with both the insurance company and FEMA they wanted a design that will meet the wildfire regulations in California. SIPs exceeded this condition and was able to provide an energy and sustainable product that exceeded all CalGreen requirements.
Structural Features of SIPs That Contribute to Fire Resistance
- OSB (Oriented Strand Board) Facing: The outer layer of SIPs is made from treated structural grade OSB, which chars when exposed to fire. This charring acts as a barrier, slowing the penetration of heat and flames.
- Insulating Foam Core: SIPs are made with solid rigid foam insulation (e.g., EPS or GPS) that does not significantly contribute to fire spread due to its polymeric flame retardant and self-extinguishing properties. Further, because the core is solid, there is very little air in the wall or roof cavities. Without oxygen to feed the fire, the spread is minimized.
- Sealed Joints: The airtight construction of SIPs minimizes oxygen flow through and within wall assemblies, reducing the ability for fire to spread internally.
- Explore more on the basic features and benefits of SIPs here.
Performance in Fire Testing
SIPS & POTENTIAL FIRE EXPOSURE: Passing critical fire tests, Premier SIPS create airtight residential and commercial structures. The airtight roof, wall and floor assemblies are known to starve oxygen, making fire much less likely to spread through interior spaces.
- Fire-Rated Assemblies: SIPs can be designed to meet or exceed fire ratings (e.g., 1-hour fire resistance per ASTM E119 standards) when paired with appropriate gypsum or cladding.
- Proven Safety in Fire Tests: SIPs have demonstrated exceptional performance in fire exposure tests, including:
-
- NFPA 285 Multi-Story Fire Test
- NFPA 251 Fire Resistance Test (20 minutes & 1 hour)
- NFPA 255 Flame & Smoke Developed Test
- UL 1256 Roof Assembly Flame & Smoke Developed Test
- ASTM E119 testing, resulting in Class A roofing system roof deck approval per ASTM E108 and UL 790.
- Supporting Data: Controlled burn testing and research consistently show that SIPs maintain structural integrity longer under fire conditions compared to traditional stick framing. These tests confirm the reliability of SIPs in real-world fire scenarios. Including from the California Fire Investigators Association, who hosted a fire demonstration to test how SIPs performed in fire situations. The results speak for themselves.
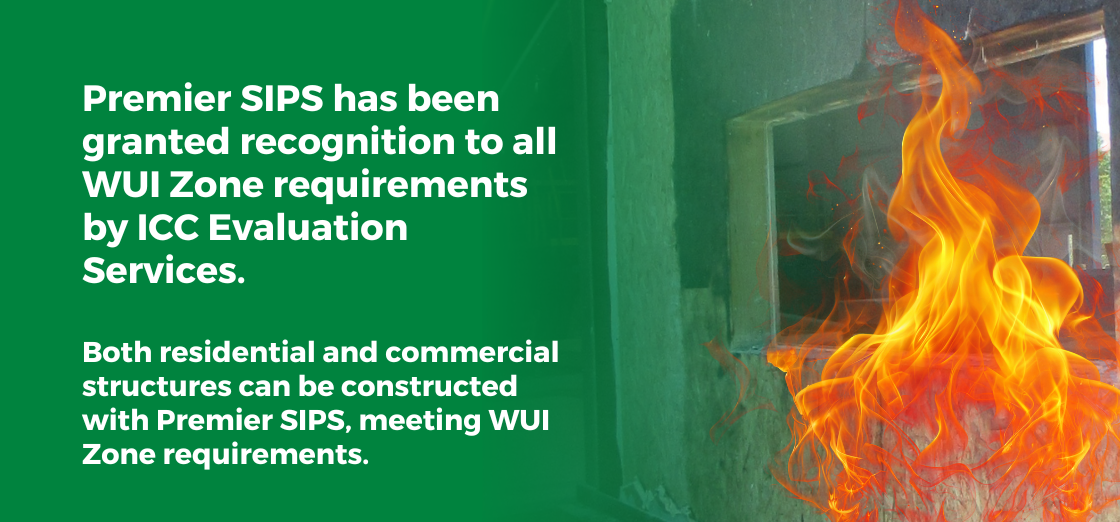
Enhanced Fire Safety Features
- Airtight Envelopes: The airtight construction of SIPs prevents the entry of smoke, harmful fumes, and fire debris into the home, even during nearby wildfires. This feature helps maintain air quality and provides residents an additional layer of safety.
- Non-Vented Attics: SIP construction eliminates the need for traditional vented attics, significantly reducing fire risk.
- No Ember Entry: Traditional attic vents often act as entry points for floating hot embers during wildfires, igniting the interior structure. SIPs create a fully enclosed attic space, preventing debris and embers from entering.
- Conditioned Space: The enclosed SIP attic serves as a usable, conditioned storage space without the fire hazards associated with vented rooflines.
- Improved Protection: By eliminating roofline venting, SIP attics also block oxygen pathways that would otherwise fuel a fire.
- Slower Heat Transfer: The insulation core and continuous construction reduce thermal bridging, slowing heat transfer through the building envelope and minimizing heat spread in the event of a fire.
- Minimal Combustible Material: SIPs have fewer voids and cavities than traditional stick framing, reducing areas where fire can gain a foothold and spread.
⇒ SIP Project Highlight: In the '90s, Oakland Hills, California, faced a devastating and fast-moving firestorm that quickly flattened homes. SIP walls and roofs, being solid cavity panels, have minimal air movement within the building enclosure, unlike traditional stick and batt framed assemblies. This design means there was little oxygen available to "feed" the fire's spread through the SIP structures that remained standing as the fire ravaged the neighborhood.
Fire-Resistant Design Applications
- Fire-Rated Design Assemblies: SIP assemblies combined with 1-hr fire rated materials such as Fiber Cement siding, stone/stucco or metal cladding, add in Class A tile flooring and fire-rated windows and doors can deliver a fire resistant structure. Essentially you are designing with specific materials that encase a SIP thermal building enclosure that is already fire rated on its own.
- Exterior Fire-Rated / Fire-Resistant Treatments: SIPs can also be treated with various fire rated topical treatments to achieve additional fire rating requirements for use in specific applications such as multi-family projects. Contact your regional rep, to learn more about the treatments available for safety codes in your region.
Building Code Compliance
- Premier SIPS ICC ESR-4524 Updates: Premier SIPS consistently meets and exceeds the latest building code requirements, ensuring safety, performance, and compliance. Key updates include:
- 1-Hour Fire-Rated Wall Assembly: Rigorously tested per ASTM E119 standards, Premier SIPS achieve a 1-hour fire rated assembly for thicknesses ranging from 4.5” to 12.25” and heights up to 24 feet - offering versatile fire safety solutions for residential and commercial applications. See Technical Bulletins F1 and F2 for more specifics.
- Wildland-Urban Interface (WUI) Standards: SIPs meet many of the fire safety standards required for residential and commercial construction in wildfire-prone areas, such as California’s WUI codes.
- Compliance with 2021 International Codes: Fully recognized under the IBC (International Building Code), IRC (International Residential Code), and IECC (International Energy Conservation Code) energy efficiency standards.
- California and Los Angeles Code Recognition: Premier's SIPs are in compliance with the California and Los Angeles Building Codes for both residential and commercial structures, making Premier SIPS an excellent choice for wildfire-prone areas and other high-risk zones.
⇒ Project Highlight - Enchanted Hills Lighthouse Camp for the Blind: "This camp was burned out in the CA wildfires in Napa. By utilizing SIPs on the roof, the rebuilt camp was able to achieve the stringent fire codes in the area, gain significant energy efficiency over the burned-down buildings, and enabled the camp to resume operations much faster than anticipated because of the speed of construction SIPs delivered." - Client (View Project Here)
Real-World Benefits
- Safer Evacuation: Fire-resistant SIP structures can provide occupants with more time to evacuate during a fire.
- Post-Fire Rebuild Efficiency: SIPs’ prefabricated nature speeds up rebuilding timelines in communities affected by wildfires as construction with SIPs is regularly twice as fast as traditional stick-framed construction because much of the labor being done in the factory.
- Insurance Benefits: Fire-resistant SIP structures may qualify for reduced premiums in areas prone to wildfires.
-
Tax Incentives: SIPs can help projects qualify for federal and state tax incentives, such as the 45L tax credit for energy-efficient homes, providing additional cost savings for builders and developers.
⇒ Fire-Departments all over North America are built with SIPs because of their fire-resistive properties. Take a peak at some of the fire and emergency stations, in our portfolio (many more not pictured!).
Environmental and Economic Impact
- Long-Term Resilience: The inherent strength and durability qualities of SIPs help not only in fire-prone areas, but also in other natural disaster zones including seismic, and hurricane concerns. SIP construction reduces the likelihood of total structural loss, minimizing the need for rebuilding and conserving natural resources. [Learn About The Strength Of SIPS]
- Waste Reduction: SIPs’ precision-engineered panels minimize construction waste both on-site and in manufacturing, contributing to cleaner job sites and less landfill use. [Learn More]
- Sustainability & Carbon Footprint Reduction: SIPs contribute to energy efficiency, reducing operational energy use and lowering greenhouse gas emissions over the building's lifespan. [Learn More]
Key Resources
Connect with your local Premier SIPS representative today to explore how SIPs can be integrated into your next project. From fire performance insights to tailored design solutions, we’re ready to support your vision for safer, more resilient construction. Let’s build the future together.
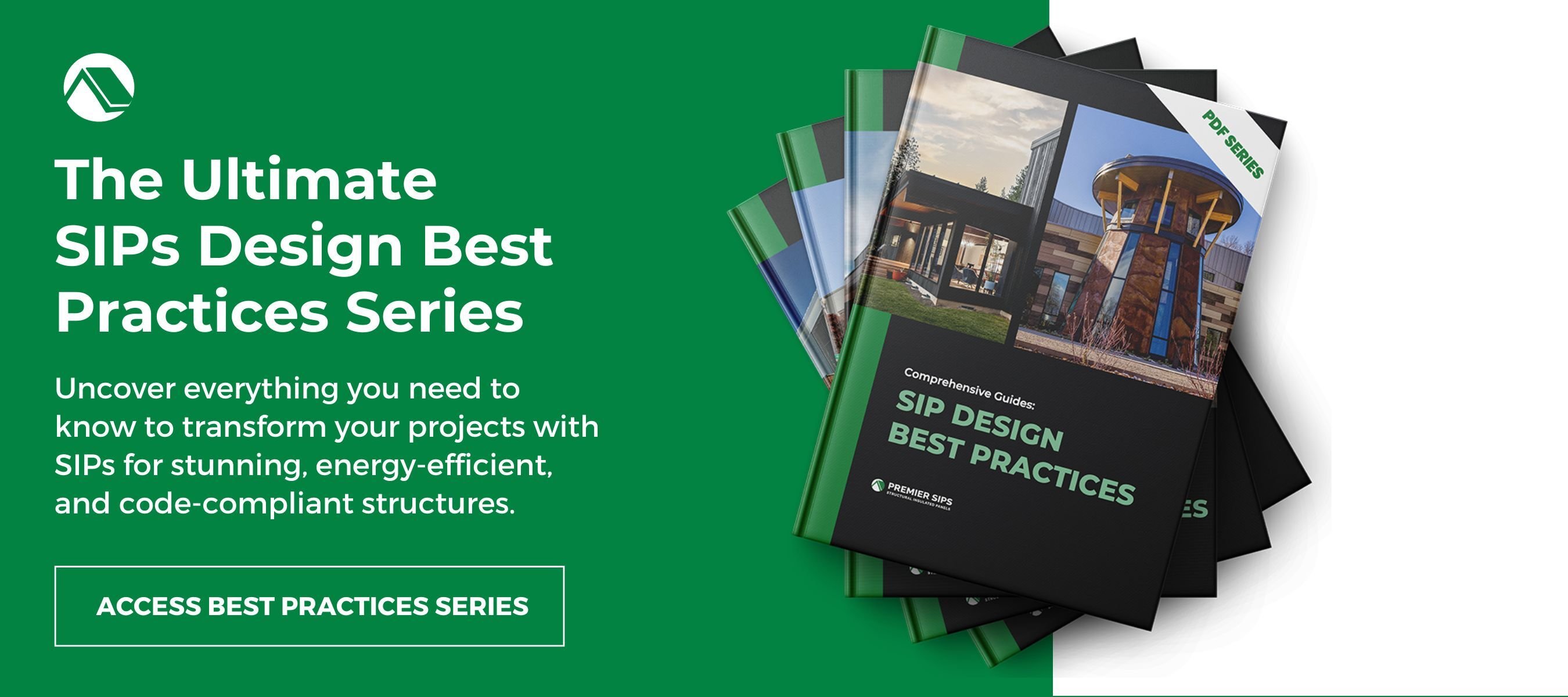