Alakanuk School
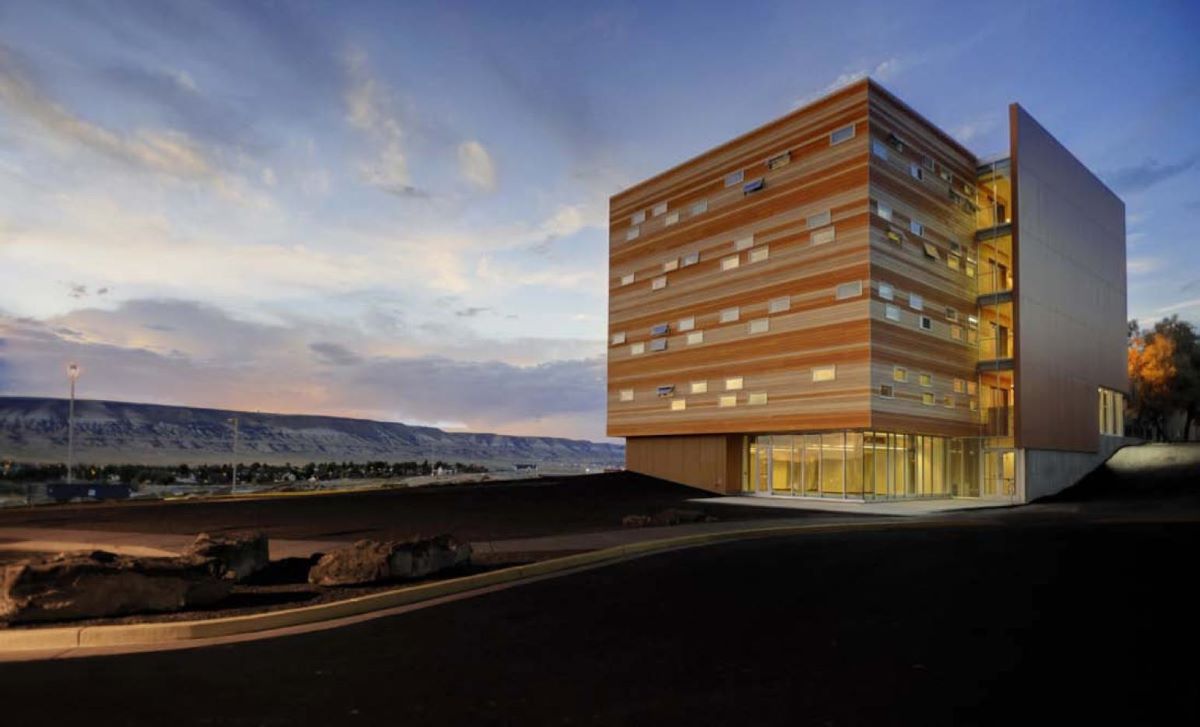
Western Wyoming Dorms, Rock Creek, WY
Wyoming
Project Type Commercial | Education/Schools
Year Completed 2008
Project Size 28000 sq ft
SIPS Used Roof & Walls
Environmental Certifications LEED/USGBC
Project Overview
When the 2008/2009 school year kicked off at the Western Wyoming Community College (Western) in Rock Springs, WY this fall, students were greeted by a new state-of-the-art, 28,000-square-foot housing complex that features 48 bedrooms spread throughout four stories. Wind River Hall has everything a college student could ask for, including 12 individual bedrooms, six fully functional kitchens and three spacious living rooms per floor.
Before Wind River Hall was designed, extensive research was conducted at institutions throughout the United States to determine student preferences regarding residence hall room arrangements. “Many students expressed the desire to be social yet also have the opportunity for privacy. Wind River Hall is designed with these wants in mind,” said Jon Schrade, Western’s Director of Housing and Student Activities.
While Wind River Hall meets the need for both social and private spaces through a spacious layout, it is the building’s innovative construction that truly makes it unique. Framed entirely out of structural insulated panels (SIPs) manufactured by Premier Building Systems in Fife, WA, Wind River Hall is the tallest self-supporting SIPs structure ever built.
Consisting of an expanded polystyrene (EPS) insulation core sandwiched between two layers of oriented strand board (OSB), SIPs are a dependable, cost-effective building solution that address four issues on the minds of virtually every school official involved in the construction process – energy efficiency, lifecycle costs and both environmental and indoor air quality.
Energy Efficiency
Buildings account for nearly 30% of all energy consumption in the United States. As oil and gas prices continue to rise, many publicly funded schools are experiencing higher than expected heating and cooling costs that are cutting into their delicate budgets.
SIPs are used in lieu of traditional framing materials such as wood and steel studs. Studies conducted by the Oak Ridge National Laboratory in Oak Ridge, TN, have shown that SIPs can help reduce a building’s annual energy costs by 50% - 60% when compared to more common framing methods.
Because of their energy efficiency, SIPs are also recognized by a number of governmental groups, including the Environmental Protection Agency (EPA) and the Department of Energy (DOE). The ENERGY STAR® program, administered by the EPA, has waived the need for a blower door test on any building constructed with SIPs. DOE officials have also said that the $2,000 Federal Energy Tax Credit is virtually impossible to gain without SIPs.
Lifecycle Costs
While energy savings are the most obvious benefit of using SIPs, this product also provides numerous other opportunities for building owners to improve their return on investment by reducing a building’s lifecycle costs.
SIPs are prefabricated to the exact specifications of a project and delivered to the job site ready to install. This results in a more efficient installation and helps eliminate the costly removal of construction waste. SIPs are also easier and more efficient to install than competitive systems, reducing construction time and minimizing labor costs.
In addition to enhanced time and energy savings, SIPs provide more strength and durability than stick- and steel-framed buildings. The increased durability is ideal for college environments, where students often take advantage of their newfound independence by turning campus buildings into their own personal punching bags. With SIPs, colleges get a dependable, long-lasting structure that can withstand constant abuse.
SIPs may also allow for a reduction in the size of a building’s HVAC equipment by up to 40%, which means lower upfront costs for equipment purchases and a reduction in future maintenance costs.
Environmentally Conscious
Colleges are increasingly turning to green building practices as a way to entice new students, reduce their carbon footprints and receive government grants, subsidies and tax incentives.
By utilizing SIPs, buildings can earn up to 23 points within the LEED Green Building Rating System™, the nation’s predominant green building program administered by the United States Green Building Council. SIPs also contribute to the $2,000 Federal Energy Tax Incentive, as well as a number of other tax programs that can help put money back into a university’s budget.
Improved Indoor Air Quality
The EPA lists poor indoor air quality as the fourth-largest environmental threat to our country, a problem that is often overlooked during the construction process. Recent studies indicate that poor indoor air quality can have significant effects on respiratory illnesses as well as the overall health, achievement and productivity of a building’s occupants.
The best way to mitigate the causes of poor indoor air quality is to create an airtight building envelope. The airtight nature of SIPs helps improve indoor air quality and reduce unwanted air transfer by reducing gaps in the building envelope.
An unsealed building envelope allows unwanted infiltration of common pollutants such as radon, molds, pollen, VOC’s, lead dust and asbestos. By using SIPs to protect the indoor environment from these toxins, colleges can improve the health of their student body while providing them with the best possible atmosphere for educational success.
Related Portfolio
Find Your Local Rep
As the oldest SIP manufacturer, Premier SIPS offers a superior building envelope framing system for commercial and residential structures. Contact an expert in your region to discuss your next project or to explore the benefits and cost savings when designing and building with SIPs.