Alakanuk School
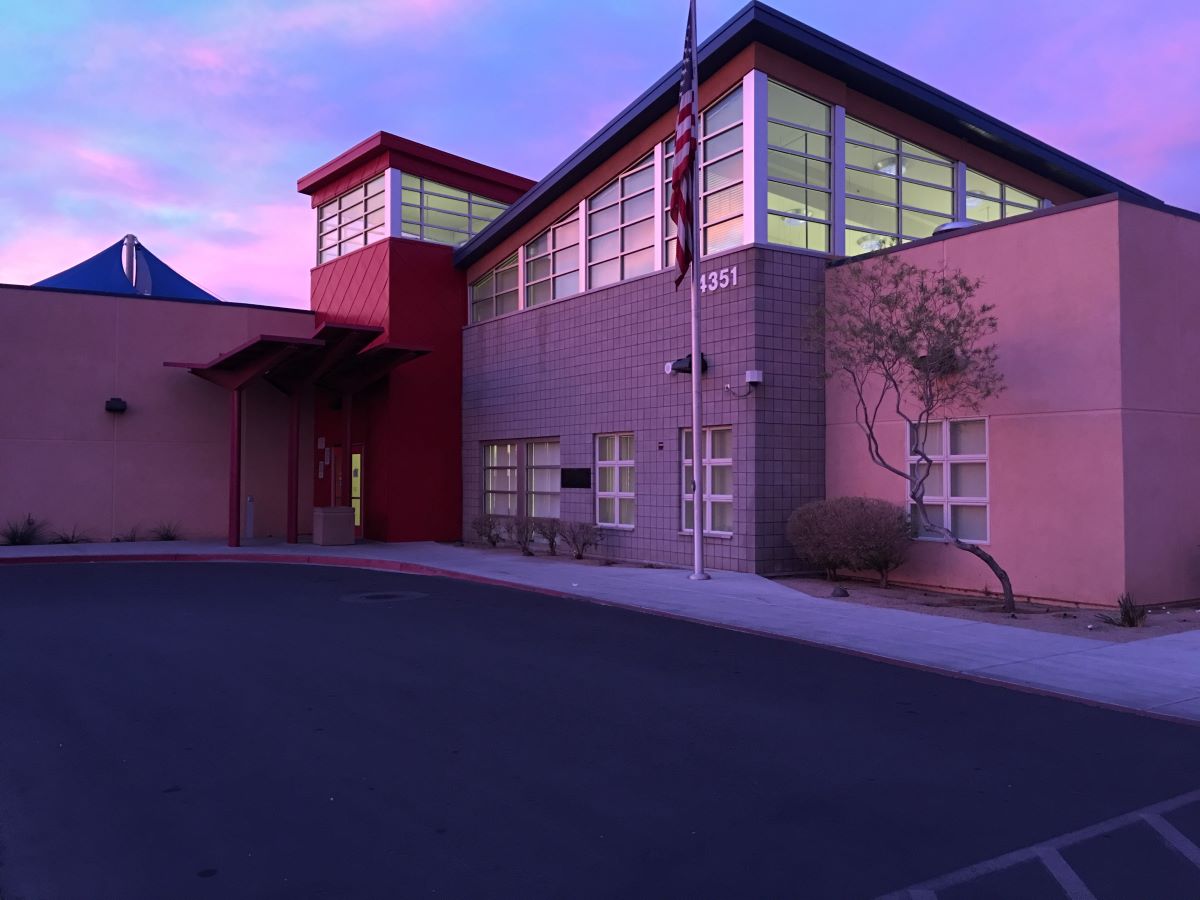
Educational | Nevada | SIPs Elementary School
Nevada
Project Type Commercial | Education/Schools
Year Completed 2009
Project Size 68000 sq ft
SIPS Used 118,000 sf Roof & Wall SIPs
Awards 2019 SIPA Building Excellence Overall Competition Winner
Architect SSA Acrchitecture
Contractor Martin Harris Construction
Project Overview
“This was the fastest form of construction we have ever used, we have built with CMU, Steel, Wood framing, you name it and these SIPs were the best thing we have ever experienced on a job of this magnitude.” – Martin Harris Construction
School districts across the United States are increasingly under pressure to manage capital construction and operating costs. When new or remodel construction is needed, many face numerous hurdles, including rapid student population growth requiring larger facilities, and limited funding from local tax levies to pay for building development, along with energy costs to provide a conducive learning environment.
When Clark County School District (Las Vegas, NV) began to plan a new elementary school with a tight budget and construction schedule, project architects SSA Architecture of Las Vegas recommended incorporating structural insulated panels, SIPs, in all exterior walls and roofs for a more efficient and systematic approach to the building’s structure.
The Jacob E. Manch Elementary School is a replacement for an existing building originally constructed in 1963. During the preliminary design stages, the architects determined that materials customarily used in the district – primarily concrete masonry units (CMUs) and tilt-up concrete panels – would not be cost feasible within the approved $20M budget. In addition, with rapidly rising energy costs, the school district was looking for a solution that would reduce heating and cooling demands.
Serving the families around Nellis Air Force Base, Manch is designed to support 900 students in a year round multi-track schedule. After the school district awarded the project to SSA Architecture in 2004, market conditions increased the estimated construction costs (approximately 1.5 percent per month in the then booming Las Vegas construction market).
During the programming and preliminary design stages, the architects determined that materials customarily used in the district – primarily concrete masonry units (CMUs) and tilt-up concrete panels – would not be cost feasible within the approved budget. In addition, with rapidly rising energy costs, the school district was looking for a solution that would reduce heating and cooling demands. CMUs and concrete walls typically do not perform well thermally in the extreme heat and cold of the Las Vegas desert. During extended periods of the year, they absorb heat under daytime temperatures that often reach 110 degrees Fahrenheit or greater, without the opportunity to cool down at night. The result is a high burden on cooling systems. The school site is also regularly impacted by jet aircraft noise from the nearby air force base. The roar of military jet engines creates intense bursts of sound that distract student learning. Adding further complexity to these challenges, the school district needed the replacement school completed as rapidly as feasible to minimize disruptions to students and teachers still using the existing adjacent school.
To meet the various program and construction challenges, the architects specified structural insulated panels (SIPs) for all exterior load-bearing walls and roofs. Structural insulated panels (SIPs) are an easy-to-use and environmentally friendly advanced framing alternative to traditional construction. Composed of two sheets of oriented strand board (OSB) structurally laminated and pressure-cured to a rigid core of expanded polystyrene (EPS) foam insulation, SIPs are strong, straight and predictable, and provide superior insulation.
SIPs have been used in a range of commercial, institutional and residential buildings for decades, and have become more prevalent in recent years as architects, contractors and building owners learn more about their benefits. They are approved for used by every model building code in the U.S.
The architects report that in terms of interior thermal conditions, SIPs make the building perform like “a big refrigerator box.” This drops HVAC costs substantially. SIPs also typically have a far reduced sound transmission, allow more flexibility in locating skylights, and install far faster than any of the other technologies typically used for schools.
Similar projects using concrete materials typically require about 118 to 220 days to be “dried in,” ready for interior finishing work. With SIPs, the time was reduced to 45 days – up to approximately 80 percent less time.
According to Shell Building Systems, a Premier SIPS distributor and consultant for Manch design and construction, SIPs install faster, save on structural building time, and reduce labor time for the electrical work. The panels have electrical chases built inside them so electricians don’t have to drill or modify faming. Instead, they can easily pull wires through the chases which include 1” vertical chases at 16” on-center, and horizontal chases at the exact elevations needed for the electrical outlets.
The general contractor was shocked at how fast the panels installed – he said he’d never seen that size of schedule reduction. including the time savings on electrical work. In addition to offering fast and easy installation, the Premier SIPs provide superior insulation. The foam core serves as an insulating layer, and compared to stud framing, the large one-piece panels have fewer gaps needing to be filled and sealed. Using SIPs cuts down on energy-related costs two ways, there’s less demand for heating and cooling, so HVAC systems can be substantially smaller, saving on equipment costs. Plus, the ongoing costs to run the equipment are much less. Consultants for Manch School estimate SIPs helped reduce the HVAC load requirements by approximately half. The efficient building envelope SIPs help create reduces the cycling of the air conditioning units substantially, thereby further increasing the life of the equipment by about 75 percent.
Compared to alternative construction materials typical for schools, such as concrete masonry units (CMUs) and tilt-up concrete panels, the SIPs provided a number of benefits:
- Saved approximately one million dollars in direct construction costs
- Reduced the framing schedule from a typical 118 – 220 days to 45 days (a nearly 80 percent time savings)
- Reduced HVAC requirements by approximately half, providing both initial capital savings and lower annual heating and cooling bills
- Decreased construction materials waste and resulting disposal fees and environmental impacts
- Reduced interior noise coming from nearby Nellis Air Force Base bility, estimated for a fe in the school application between 50 – 100 years under nominal maintenance.
In addition, SIPs are an advanced framing technology that provides long-term durability, estimated for a life in the school application between 50-100 years under normal maintenance.
The project won the 2010 SIPA Building Excellence Awards, National Overall Competition Winner and winner in the Commercial/Industrial/Institutional category.
View & Download Project Profile
Read Case Study from the Structural Insulated Panel Association
Read a feature on Manch Elementary from "The Construction Specifier"
Manch Elementary Won the 2018
Related Portfolio
Find Your Local Rep
As the oldest SIP manufacturer, Premier SIPS offers a superior building envelope framing system for commercial and residential structures. Contact an expert in your region to discuss your next project or to explore the benefits and cost savings when designing and building with SIPs.