Custom Residence, AK
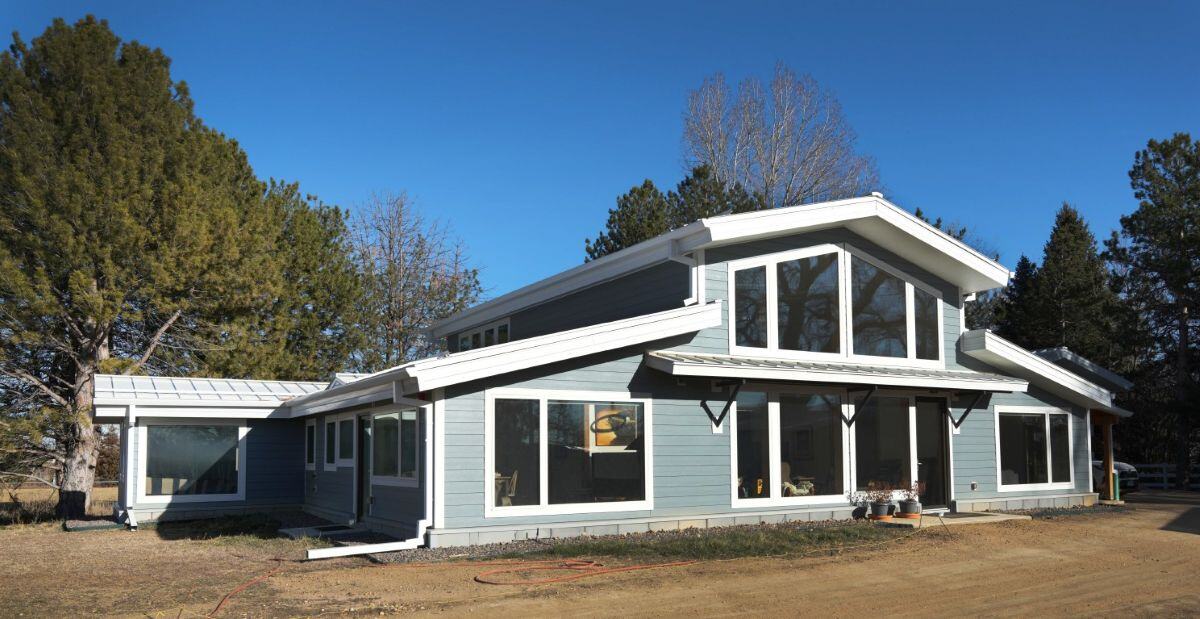
Residential | Colorado | SIP Single Family
Colorado
Project Type Residential | Single Family < 3000 sf
Year Completed 2024
Project Size 3274 sq ft
SIPS Used 6" EPS Walls - House / 4" EPS Wall Garage - 12" EPS Roof House - 10" EPS Roof Garage
Sustainable Features Premier SIPs, converted old airplane hangar into barn, deconstructed original structure and reused or recycled materials
Environmental Certifications Energy Star Certified
Awards 2025 Building Excellence Award Runner Up High Performance Residential Over 3000K S/F
Architect SH-6 Architecture + Design
Contractor PG Arnold Construction
Project Overview
zero energy, all-electric farmstead. The passive solar residence has all the modern conveniences one would expect in a new home and amenities for
wool dying and a wool spinning loft. The farm residence has a conditioned living area of 3274 SF. The attached garage adds another 1166 SF.
electric or come from non-carbon sources and power needs would be largely offset by active and passive solar. We entertained everything from straw bale
construction, straw and clay construction, earth blocks, double wall framing, etc….weighing out the embodied energy, maintenance schedules, costs and
longevity of each option. Ultimately SIP construction became the obvious choice.
detailing for airtight envelopes we were able to meet the exacting specifications of high performance insulation and airtightness levels necessary to
achieve a HERS -26.
overhangs, a ventilated rainscreen wall assembly and cap it off with a ventilated cold roof – which helps to keep it warm and dry. The goal was to
minimize drying time for the water and vapor that makes its way into the wall and roof assemblies over the life of the structure.
The roof eaves were extended to control bulk water and optimize passive solar gain on the south elevation. The rainscreen siding assembly and a cold roof
were designed to allow the cementitious siding to dry inwards and outwards by providing a ventilation gap between the cladding and the SIP skins so moisture wouldn’t become trapped. The airspace allows for convective drying of any moisture so that neither the siding or SIP skins are damaged over time. On the roof we allowed for a 1.5” airspace for convective drying and cooling during the hottest months.
wildfire smoke and particulate matter (PM2.5).
panel seams as well as windows and doors was critical for success. The windows were tuned for their aspect, with the south facing window
performance values being U-.14 and SHGC .46. On all other aspects the windows were in the range of U- .14 with a SHGC of .17. The high SHGC allows a
tremendous amount of solar radiation to be captured by the specially designed thermal mass concrete floor. The concrete thickness was optimized for thickness and poured with minimal air entrainment to allow the sun’s rays to penetrate deeply in a timely manner. Imbedded in the slab is a closed loop radiant tubing system designed to distribute heat gained from the warmer parts of the slab to areas that don’t receive direct solar gain. The roof metal selected has a very high solar reflectance, designed to reflect solar heat rather than absorb it where the heat would be conducted into the envelope of the building.
Related Portfolio
Find Your Local Rep
As the oldest SIP manufacturer, Premier SIPS offers a superior building envelope framing system for commercial and residential structures. Contact an expert in your region to discuss your next project or to explore the benefits and cost savings when designing and building with SIPs.